State of the art solutions
Our portfolio is built to address the evolving needs and challenges of the industries we serve. We believe in pushing boundaries and constantly move the limits of what's possible.
Active Magnetic Balancing® System
An ideal rotor, ideally centered in an ideal stator, would lead to no radial forces. In reality no such machine exists. E.g. manufacturing and assembly tolerances, thermal expansion and aging all contribute to airgap shape deviations.
An uneven airgap creates harmful forces and fatigue and results in excessive repair needs, increased downtime and ultimately reduced service life. Conventional measures aimed at mechanically strengthening the equipment may temporarily reduce symptoms, but will never resolve root cause. Only switch downtime for downtime.
The Active Magnetic Balancing® System continuously detects and actively compensates for airgap shape deviations, maintaining your machine symmetric at all times. It literally turns your machine into a self-healing unit!
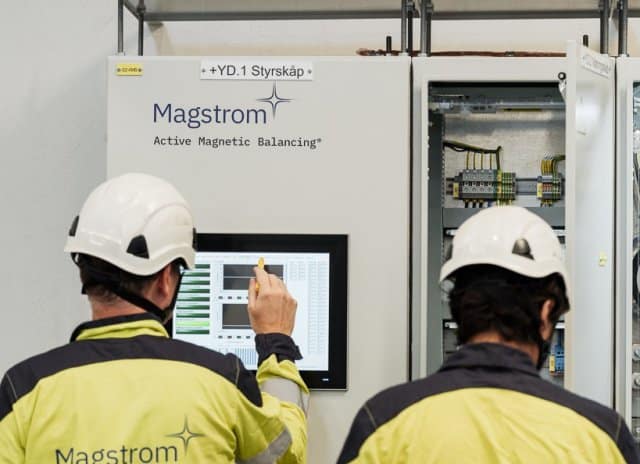
Active Magnetic Balancing® Explained
The Active Magnetic Balancing® System is a combined software and hardware solution that serves as add-on to existing excitation system on new and used equipment. Magnetic flux density sensors continuously measure rotor and stator roundness as well as individual rotor pole strength. They further help detect e.g. a rotor pole interturn short circuit or a broken damper bar.
The system uses the existing rotor poles as controllable electromagnets and with help from power electronics generates the balancing currents needed to neutralize harmful forces that arise due to airgap shape deviations. The power electronics are applied either as fully rotating or mounted on the static side, all depending on the machine’s conditions and needs.
Regardless of topology the end result will always be the same: The machine remains magnetically symmetric and in ‘better than new’ conditions at all times!
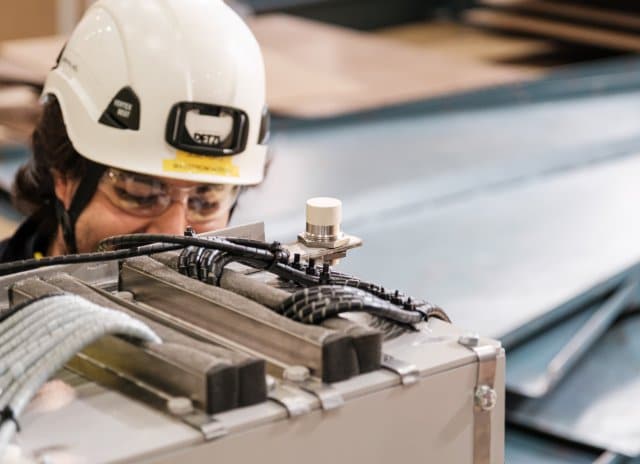
The Value Proposition
The Active Magnetic Balancing® System offers true value throughout the entire lifecycle of a synchronous generator or motor, starting already during design and manufacturing when incorporated in new equipment. By neutralizing the same forces that much of conventional design work aims to counteract, the mechanical tolerances can be relaxed and the design be made more cost-effective and substantially less carbon-intensive.
The main benefits of the system derives from drastically reduced needs for unplanned maintenance and repairs and its related downtime. It’s further common for Active Magnetic Balancing® to help lift production restrictions that were imposed on a machine due to issues with vibrations or uneven heat distribution. Last but not least, the system can extend the service life of mentioned equipment by an estimated 20%. The additional +10 years that this means for e.g. a hydropower generator dramatically changes the view of asset management, where the renewal of an aging fleet on mature market represents a financial burden that can now be postponed and spread out over time.
To summarize, the value proposition and return on investment depends on the situation and unit in question.